The Importance of Sensors in Manufacturing
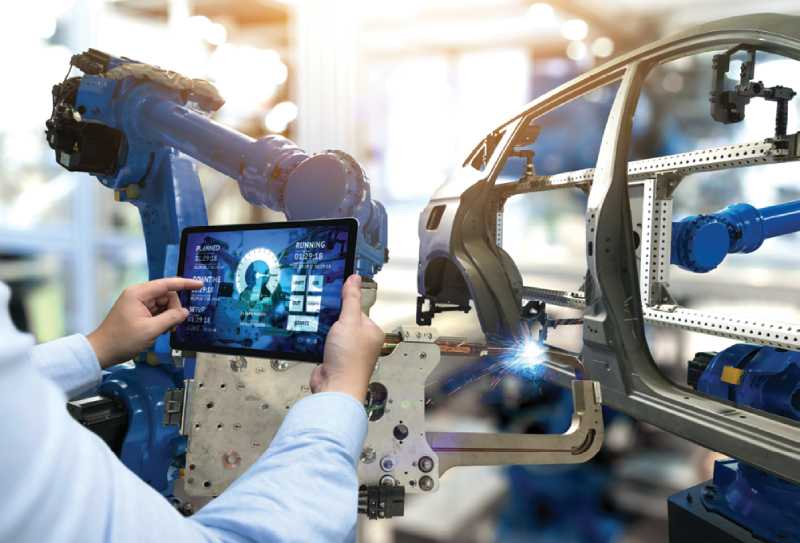
The Importance of Sensors in Manufacturing: What is a Sensor? Let’s start with ourselves and consider that our eyes, ears, nose, and touch and taste receptors all perform important tasks for our bodies to function properly, respond intelligently, and function independently. With their help, we can even maintain our balance, measure temperature and even stay in touch with such complex and sensitive human systems as monitoring blood acidity.
Table of Contents
What is a manufacturing sensor used for?
Just as an ultrasonic sensor “sees” using sonar-like technology, or a microelectromechanical sensor converts a mechanical signal into an electrical signal, the almost endless possibilities of sensor manufacturing play a similar role in responding to physical inputs such as light, movement, heat. , pressure, vibration, humidity and a variety of other stimuli. Responses to these phenomena are usually converted into a signal and are often made readable by us or transferable for automation purposes.
As our incredible 21st century progresses, sensor technology becomes more impressive and ever-evolving, and the market offering accessible through companies like RS Components is enormous. As a result, manufacturers have an increasingly unprecedented level of knowledge about what is happening in their systems, leading to greater efficiency, higher production and higher profits.
How sensors benefit the Industry?
As this technology advances, so does the exponential number of critical data points it can provide to manufacturers. While previous sensor technologies could provide a single reading at a localized point, today’s advancements are driving innovation and efficiency by exponentially monitoring machines and systems through a nearly infinite number of data points.
- Modernly manufactured sensors:
- Identify failures, errors and tolerance limits
- Recording and reporting function
- Monitor system calibration and predict errors
- Providing data to feed into integrated systems to minimize losses and ensure quality.
In other words, sensors transform “dumb” machines into intelligent, independent devices that can automate processes, significantly increase efficiency and make any manufacturing operation more competitive.
3 ways sensors support manufacturing
Monitoring
Efficient manufacturing operations make data-driven decisions that minimize waste and variability in production processes and improve product quality. Sensors are used to connect operating systems so that they can communicate with each other and even make automated and intelligent decisions.
Prediction
Continuous operation and maintenance can impact a manufacturer’s competitiveness and profitability. However, through the intelligent use of sensors to monitor machine and system problems, failures and required maintenance, downtime and part replacements can be minimized.
Integration
In the 21st century, “big data” is becoming increasingly popular – and sensors are doing all the hard work of collecting data. However, by collecting, processing and interpreting this data more efficiently, increasingly complex sensor and analysis systems can streamline and automate processes throughout the supply chain.
Sensor Manufacturing: Conclusion
From photoelectric sensors that count movements, vibration sensors to monitor machine status, current sensors to provide the right power, and many other types that are also on the market and evolving daily, sensors open up almost endless possibilities to the world of manufacturing.
ALSO READ: What is Quantum Safe Cryptography for Crypto Security
ALSO READ: 3 Advantages of Cloud Disaster Recovery